I had an idea for a painting “hood” to capture vapors and paint overspray for use when priming and coating small parts. I’ve seen similar things before, and thought I could make my own rather cost-effectively. At first, I was going to build a frame from scratch, but I realized I had an old metal shelf unit sitting around that I wasn’t using, because the shelves were rather weak particle board.
I figured this could be the basis of my painting hood. I did some brief research on fume hoods and found that best practice for paint booths is a minimum face velocity of 150 ft/min (chemical lab hoods are typically designed for 100 ft/min, go figure…) For this shelf, the open top of which measures 18″ x 36″, the minimum flow required to achieve this face velocity would be 675 ACFM.
I hopped off to Harbor Freight and bought one of their 8″ ventilators (rated at 1590 CFM, pressure unspecified) and a flexible air duct. The 1590 ACFM should translate into a face velocity of 353 ft/min. Then, I headed over to Home Depot and bought some additional duct pieces and a cheap furnace filter.
I cut the bottom shelf (which was warped from water damage) to have an opening for the air filter to fit over. Then I duct taped the edges of the hole to provide a better sealing surface. The furnace filter was easily secured to this with duct tape. The furnace filter will operate at an air speed of 572 ft/min.
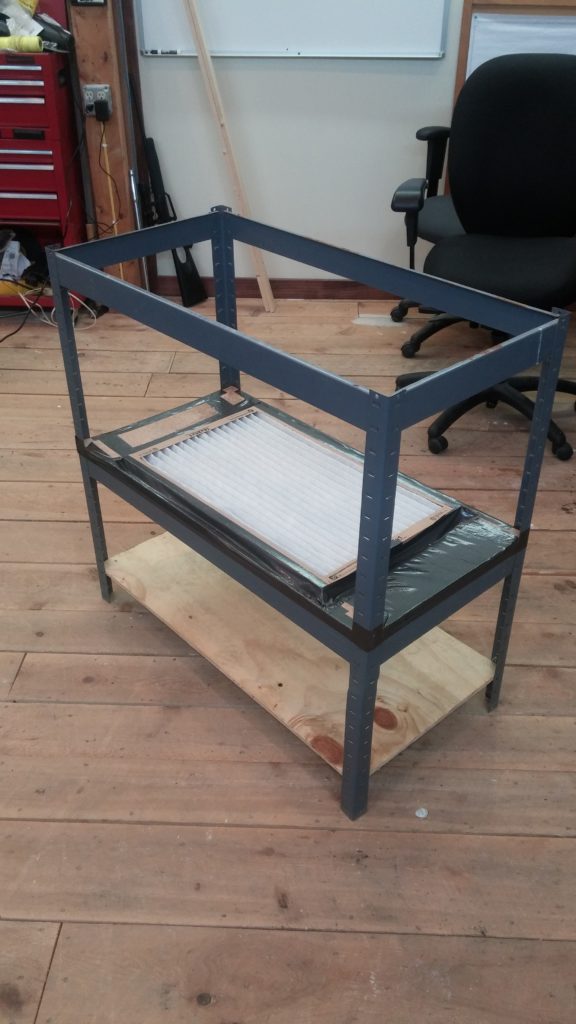
I had some duct tape and heavy (25 mil) plastic sheeting around. These, combined with the parts I had bought, and a small piece of scrap plywood, yielded this:
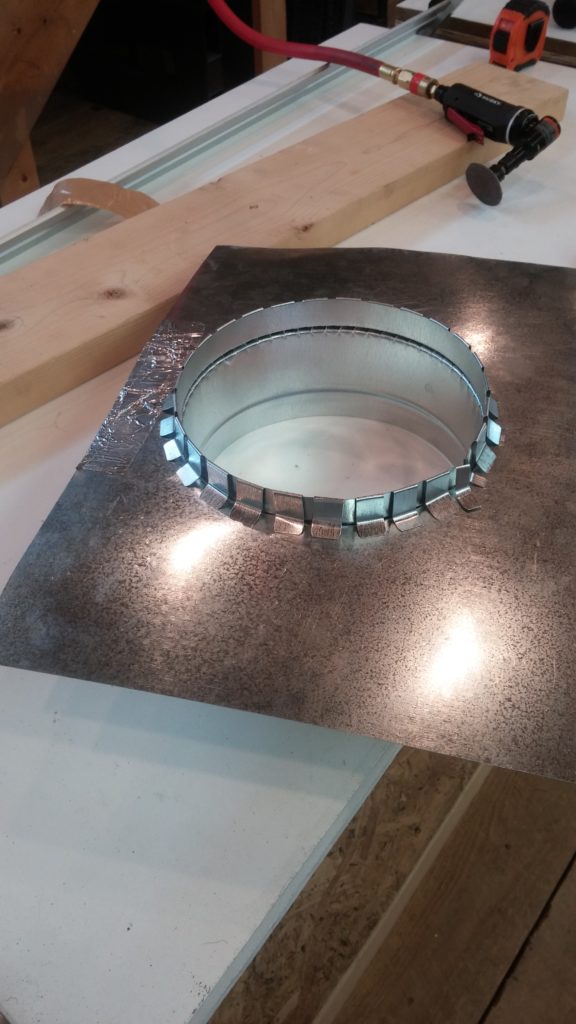
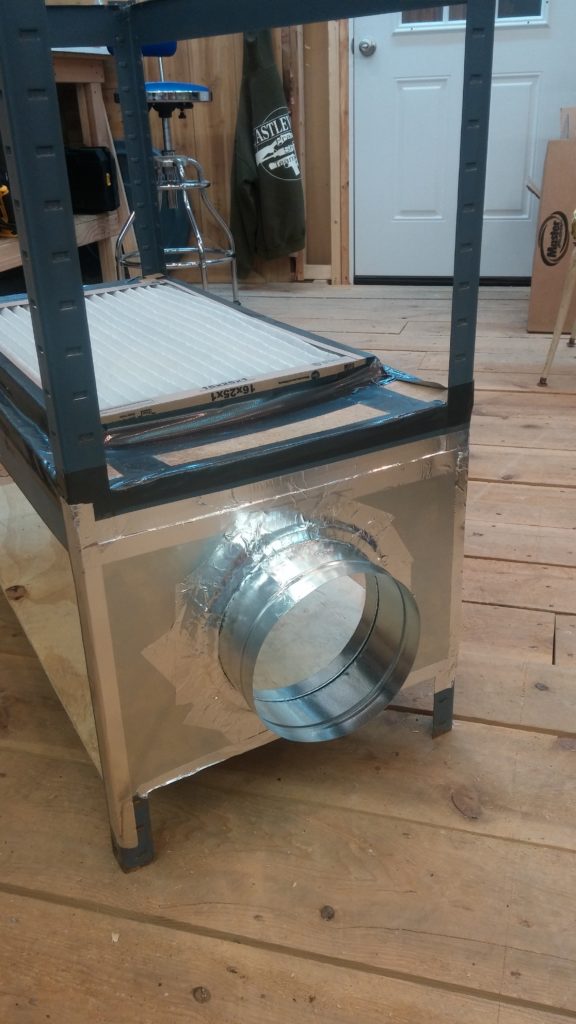
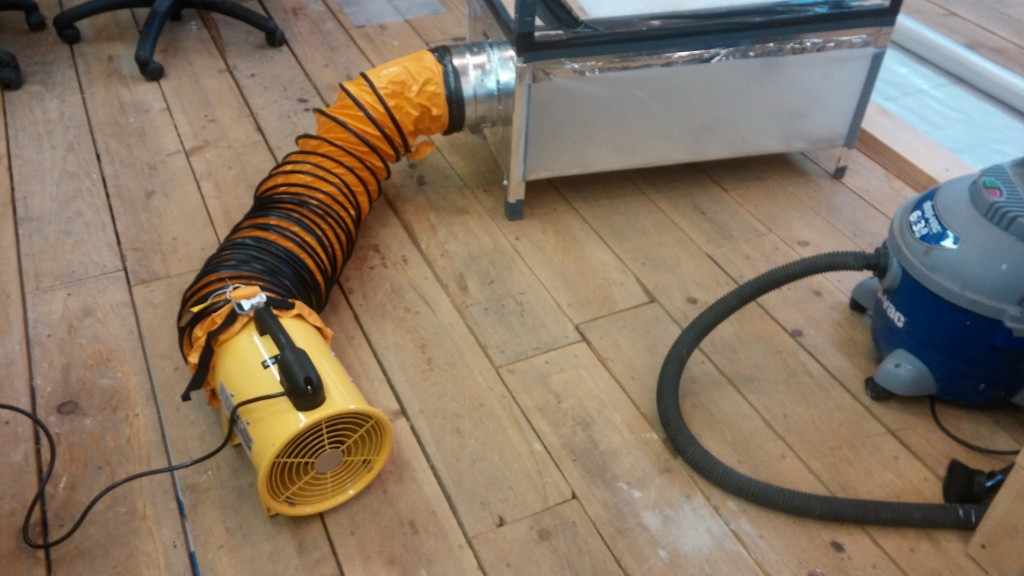
I then added a pressure tap and put my manometer to work. The differential pressure across a clean filter is almost negligible. I then covered the filter mostly with a piece of scrap plastic and the differential pressure across the occluded filter measures 0.52 inches of water column at the high speed setting on the ventilator. It will be interesting to see how much the filter changes from clean to dirty and how well it will work. I may have to use a more expensive filter rated for a smaller particle size for paint and primer.
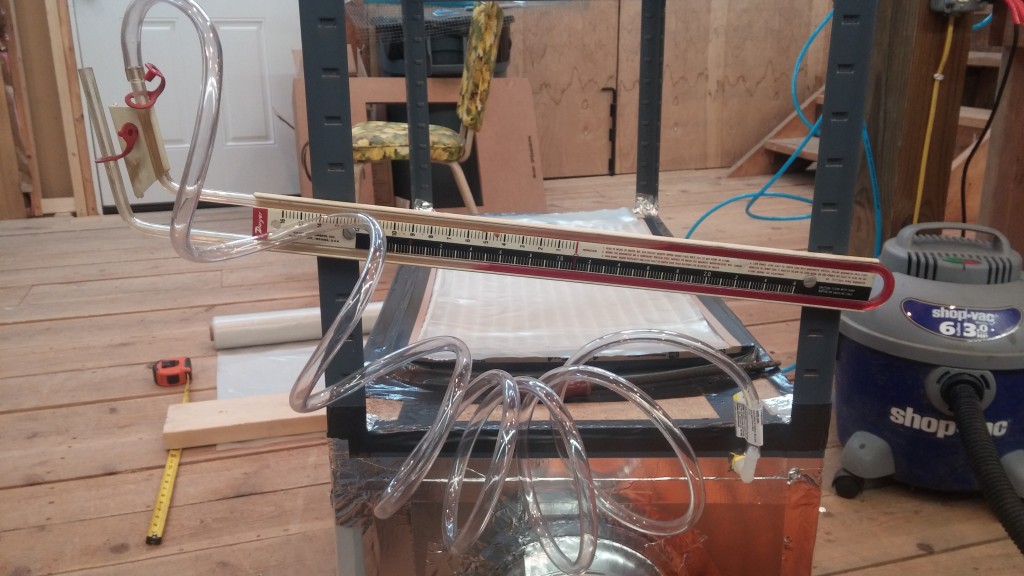
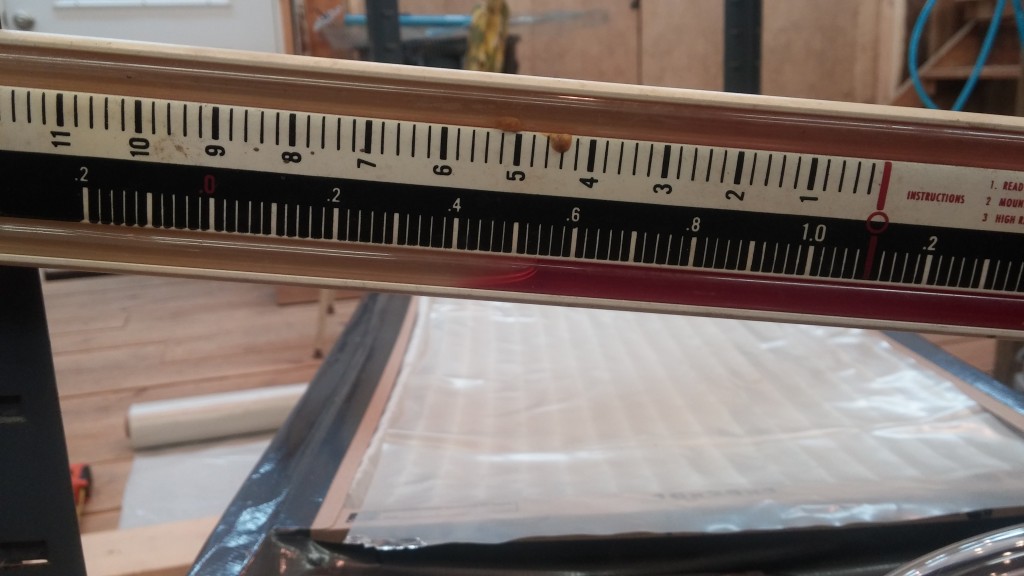
With the dP confirmed, I then finished assembling the unit with more plastic and metallic duct tape. The screen on top should allow for even painting of even small parts.
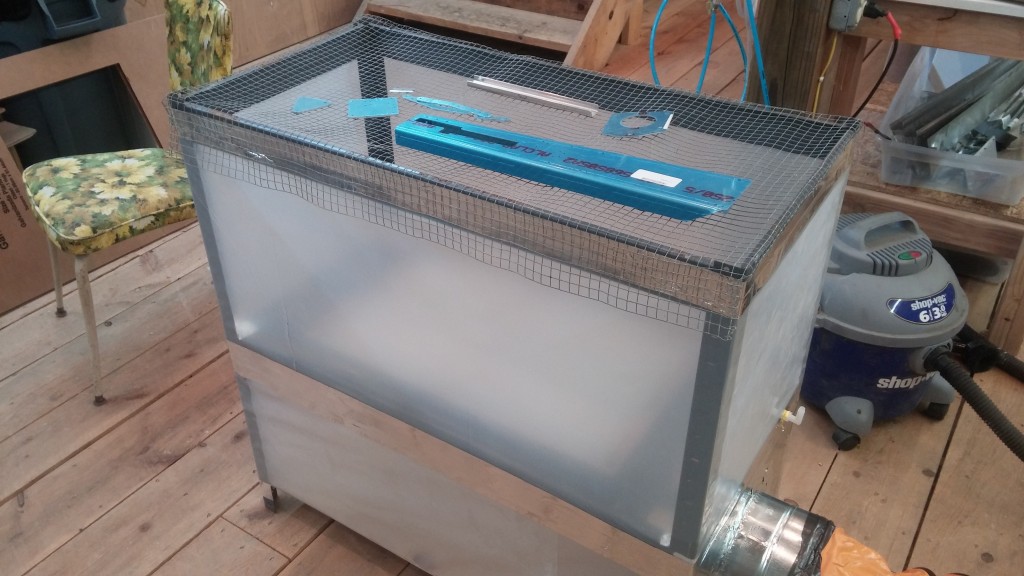
The ventilator will soon be hooked up to an exhaust duct to pipe fumes out of the workshop. Next step would be to borrow a pitot tube from work that we use to balance dust collector duct work and measure the actual air velocities in the hood and the duct.